Operations management
How relevant are the following problems to your company's Operations Management system?

Workforce shortage, high employee turnover, aging workforce, uncomfortable working conditions, increased stress in the workplace

The need for business processes reengineering and retention of changes

Long time of order fulfilment, including due to poor planning, unexpected delays, unreliable suppliers, warehouse errors

Logistics delays, including increased demand for goods, overloaded supply and distribution

Ineffective use of production and warehouse space, their unsuccessful layout

Safety level of production and warehouse areas

Labour productivity problems

Downtime of equipment and transport

Ineffective inventory management, especially in an environment with many SKUs and lack of visibility of inventories, inaccurate inventory data, changes in demand

Ineffective communication with production departments, partners, suppliers and clients

Unstable level of product and services quality

Low level of operations management
If at least one of the above statements is valid for your business, our International Management Decisions Library can help!
What is a standard operating procedure?
Management processes of any company often correspond to the well-known saying: “The new is the well-forgotten old”; In most cases, business development follows several known scenarios, so no matter how unique your management problem may seem, there is a high probability that someone has encountered the same challenge once. Clearly, albeit with some adaptation to the country and/or corporate culture, a business solution does exist that will work for you
A standard operating procedure (SOP) is a set of instructions describing in detail and systematically how to perform a task or activity related to improving business performance. These detailed guidelines are easy to follow and leave no ambiguity about what to do and how to do it. The question is, where should you look for these SOPs? The answer is …
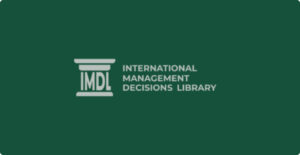